Introduction
Recently, it was reported that a large-scale strike may occur at ports
along the Eastern and Gulf coasts of the United States on October 1,
with 45,000 union dock workers going on strike and 36 ports affected.
This incident has attracted widespread attention.
As an important hub for global logistics, the operation of ports directly affects many industries.
In addition to fruits, clothing, daily necessities, automobiles, etc.,
the transportation and delivery of large equipment,
such as packaging machines, may lead to rising transportation costs,
backlogs at ports that cannot be delivered on time, and other problems,
further affecting economic stability.
1. How Ports Work
Ports are important transportation hubs connecting one land to another, responsible for the loading, unloading, storage and transshipment of goods. The workflow of ports mainly includes the following steps:
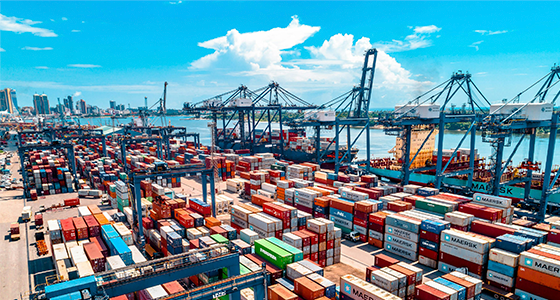
- Receiving and storing
When the packaging machine arrives at the port, it first goes through the receiving link to conduct a preliminary inspection of the machine. Qualified machines will be transported to the designated storage area. At this stage, the port management system will record the cargo information to ensure the effectiveness of tracking and management.
- Loading and unloading operations
Loading and unloading is the core operation link of the port, which is usually carried out using heavy equipment such as cranes and forklifts. For large equipment such as packaging machines, the loading and unloading process needs to pay special attention to its weight and size to ensure safety. The dock workers will use special equipment to carefully unload the packaging machine from the cargo ship and place it in a designated area of the port for further processing.
- Customs declaration and customs clearance
All imported and exported goods must go through the customs declaration process to ensure compliance with local country laws and regulations. Customs declaration generally requires the submission of relevant documents such as commercial invoices, packing lists, transportation contracts, etc. After successful customs declaration, the goods enter the customs clearance link and can only be released after customs inspection and payment of relevant tariffs.
- Transportation arrangements
After customs clearance is completed, the port will arrange further transportation according to the destination. Large equipment is usually transported by land by dedicated heavy trucks. At this time, the transportation company needs to plan the route in advance to avoid traffic jams and other possible delays.
2. The loading and unloading process and cost of the packaging machine
The loading and unloading process of the packaging machine is relatively complicated and usually includes the following steps:
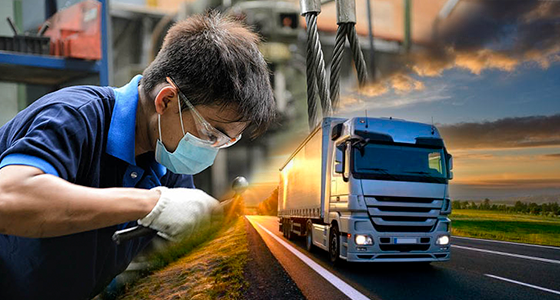
- Equipment packaging
The packaging machine needs to be professionally packaged before leaving the factory to protect the safety of the equipment during transportation. Hencin's packaging materials usually use wooden boxes, foam, protective films, etc. to avoid damage to the equipment due to vibration and moisture.
- Loading
The packaged packaging machine will be loaded onto a heavy truck by forklifts and other equipment. When loading, place the equipment well to ensure stability and use straps to fix it to avoid displacement during transportation and damage to the equipment.
- Transportation
During transportation, the transportation company will monitor the transportation status to ensure that the machines arrive safely at the destination. Depending on the transportation distance, the transportation cost will also vary, usually including fuel costs, driver wages, tolls, etc.
- Unloading and acceptance
After arriving at the destination, the machines will be unloaded and inspected. Customers need to confirm the integrity and function of the packaging machine to ensure that there is no damage.
3. The impact of port strikes on packaging machine transportation
The stagnation of ports will have a profound impact on the normal transportation of large equipment such as packaging machines
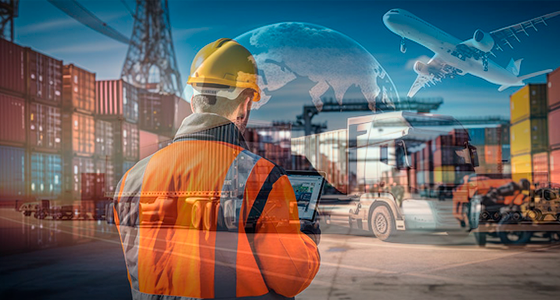
- Loading and unloading delays
The strike directly leads to the stagnation of loading and unloading operations, and the machines cannot be unloaded from the ship in time. This delay will not only affect the delivery time of the packaging machine, but also may lead to the postponement of production plans. The delivery of equipment is delayed, and customers may face the risk of production line shutdown!
- Increased transportation costs
Because the goods are stranded at the port, companies need to pay additional storage fees. These fees may include storage fees and delayed loading and unloading fees. If the transportation plan needs to be adjusted, such as switching to more expensive methods such as air transportation, the overall cost will increase significantly.
- Order backlog
Over time, orders that fail to ship on time will continue to accumulate. This will not only affect customer satisfaction, but also lead to the loss of potential customers. Long-term delivery delays may affect the company's market reputation.
- Supply chain instability
The impact of port strikes is not limited to a single region, and its impact is wide-ranging, which may lead to instability in the global supply chain. This is a huge challenge for companies that rely on international procurement and sales.
4. Strategies for dealing with port strikes
In emergencies such as port strikes, companies need to develop corresponding response strategies to reduce the impact:
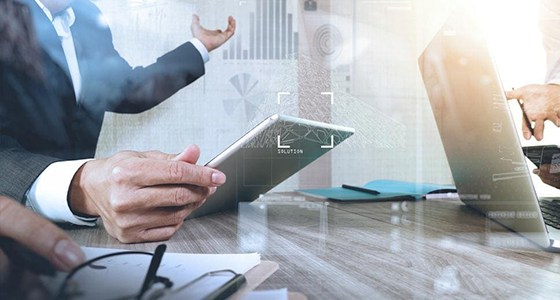
- Advance planning
Companies should be aware of possible port strike information in advance, adjust delivery plans in a timely manner, and avoid transportation during high-risk periods. You can get the latest updates by subscribing to relevant industry information and media.
- Diversified transportation channels
Consider diversified transportation methods, such as shipping through other ports, or using alternatives such as land/air transportation to reduce dependence on a single port. In addition, you can consider establishing partnerships with multiple logistics providers to increase flexibility.
- Strengthen communication with suppliers
Keep in close contact with suppliers, update transportation status in a timely manner, and adjust production and delivery plans to deal with possible delays. Regular communication helps both parties coordinate emergency plans and reduce risks.
- Flexible inventory management
Maintain a reasonable safety stock to deal with the risk of supply shortages caused by transportation delays. Companies should evaluate their own inventory levels, reasonably predict future demand, and ensure that there is enough inventory to deal with emergencies.
- Risk assessment and management
Regularly assess potential risks in the logistics chain and establish emergency plans. Through risk management, companies can better cope with challenges that may arise in the future and reduce the impact on their business.